Die Cut Box & Folding Box Packaging – Die Cut Box Design, Structure, Supplier & More
Die-cutting design is a key link in the production of die-cut box and folding box packaging, which directly affects the quality and cost of products. This design needs to consider a variety of factors, such as box arrangement, bridging and die-cutting process. Many people barely know anything about die cut box paper includes the design of die-cutting boxes, structures, materials as well as the best die cuts box supplier. Next, let’s take a look.
Everything You Need To Know About Die Cut Box & Folding Box
Compare to foldable box packaging, die cut box is suitable for containing and more solid during transportation and delivery. Most of the packaging folding cartons are the hexahedral structure, which can be divided into box surface, box bottom, box waist, box back, tongue (plug), machine (ear) and other parts. The composite packaging box materials include (1) aluminum foil spoon paperboard composite; (2) kraft paper waxing and aluminum foil composite; (3) kraft paper waxing and polyethylene film composite; (4) kraft paper, polyethylene and aluminum foil composite.
Where Can Find The Best Die Cut Box & Custom Folding Box Supplier
Kali Printing is a leading luxury die-cut box manufacturer in China. You can custom die-cut boxes with various styles possibilities for unusual cuts, slots and scores. In order to meet the demands of all customers, we offer folding paper box packaging with prime quality, environmentally friendly material, and lightweight. From folding box packaging solution, graphic design, sampling, printing to final producing, quality control as the international standard. Place an order for printed die cut boxes at wholesale price, and free samples for you to double-check.
Die Cutting Box Typographic Design
In order to reduce the cost, it is necessary to consider as much as possible to improve the utilization rate of raw material cardboard. To find a way to use the same area of paperboard to produce as many qualified cartons as possible, this problem is not the same as how to arrange as many paper blanks as possible on the die-cutting plate. Because the grain direction of the paperboard limits the placement direction of the box blank, the splicing of the box blank in the same direction is considered. The arrangement of box blank on the die-cutting plate is affected by many factors, such as the size of the box, the contour shape of the box blank and so on.
1. Flat row of box blanks
Flat arrangement is a relatively simple arrangement. When the contour of the box blank is straight, the splicing of the box blank and the box blank is relatively simple, and only needs to be arranged in parallel. For example, the beers type and the Brightwood type folding carton in the disc folding carton.
The maximum number of cartons that can be arranged along the length direction is: (1 / 1 size in the horizontal arrangement)
The maximum number of cartons that can be arranged in the width mode is: (flat size 2 / 2nd size)
The maximum number of cartons that can be arranged in the whole version is: (flat size 1)
2. Splicing of box blanks
In most cases, the shape of the box blank is not straight, which requires the box blank and the box blank to be assembled directly to improve the utilization rate. The key to nesting is to make full use of the convex and concave parts of the box blank contour for docking. It is noticed that one end of the blanks arranged in the die-cutting plate can not be spliced, and only the other end can be spliced with other blanks.
3. Bridge Design
Bridging is in order to die-cutting to the abolition of a period of time before and after, cut the carton will not fall off from the cardboard, and the abolition, the carton and waste are easy to separate, so the bridging part can not be too large, too much, otherwise it will lose the significance of bridging. It can be said that the quality of bridging directly determines whether the die-cutting process can be carried out smoothly.
The number of bridging also determines the length of the die cutter. Obviously, the less the number of bridging, the larger the average length of each section of cutter, the easier the cutter is to bend and deform, and the easier it is to be damaged in the process of reproduction. This has a great impact on the smooth operation of the die-cutting process, long tool means that in the process of die-cutting production, it may cause more frequent downtime to replace tools.
For the above considerations, the appropriate increase in the die-cutting plate bridging to solve these problems. Increasing the number of bridges can shorten the length of the die cutter, increase the strength of the die cutter, and is not easy to bend and deform. And because the length of each section of the die-cutting knife is shortened, the degree of thermal expansion and cold contraction is also reduced, and the die-cutting accuracy is reduced.
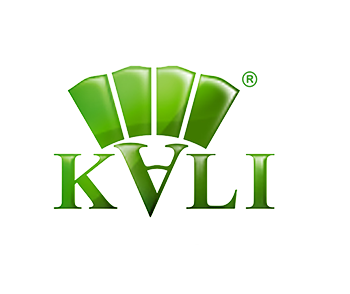
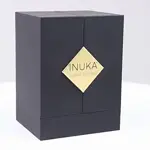
Top 10 Creative Cosmetic Packaging Design Ideas & illustrations 2023 | Luxury-Paper-Box.Com
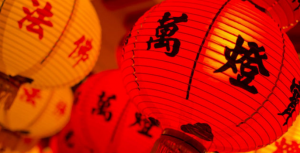
10 Customs Of The Spring Festival (Lunar New Year) You Need To Know
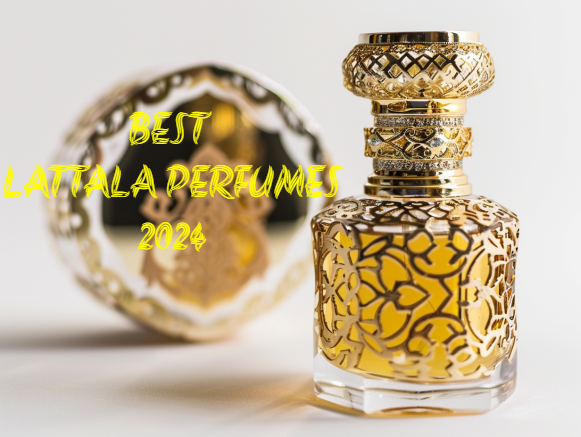
Top 10 Best Lattafa Perfumes for Women & Men in 2024
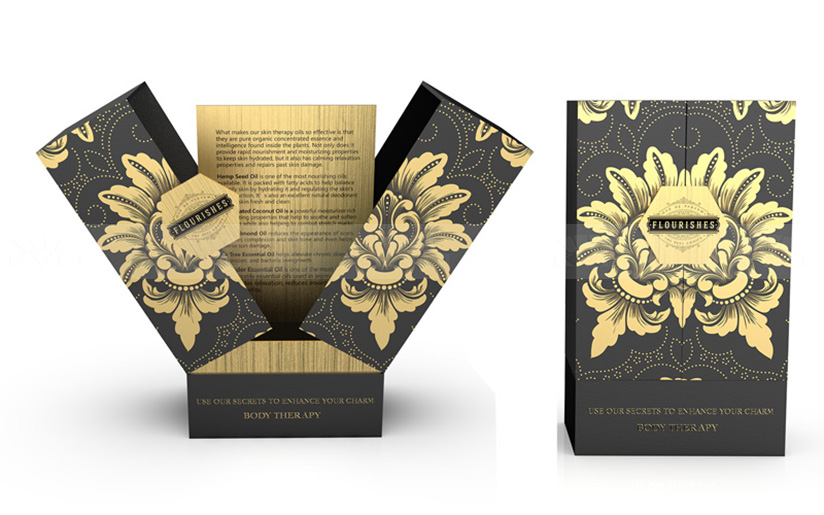
Top 10 Best Packaging Design Software 2023 (Free & Paid)
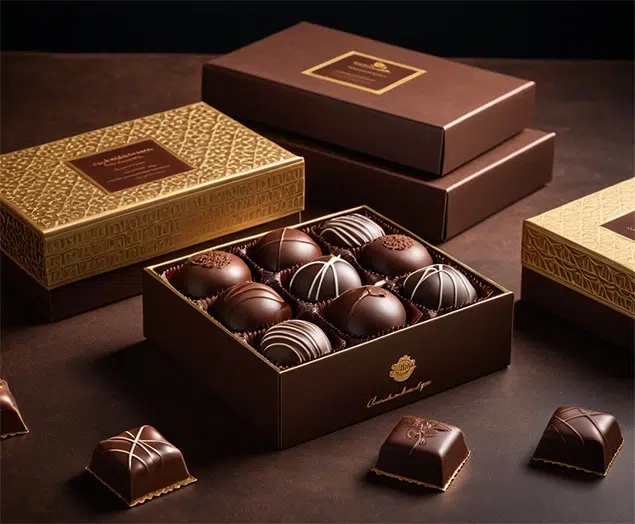
Best Chocolate Packaging Designs of 2025
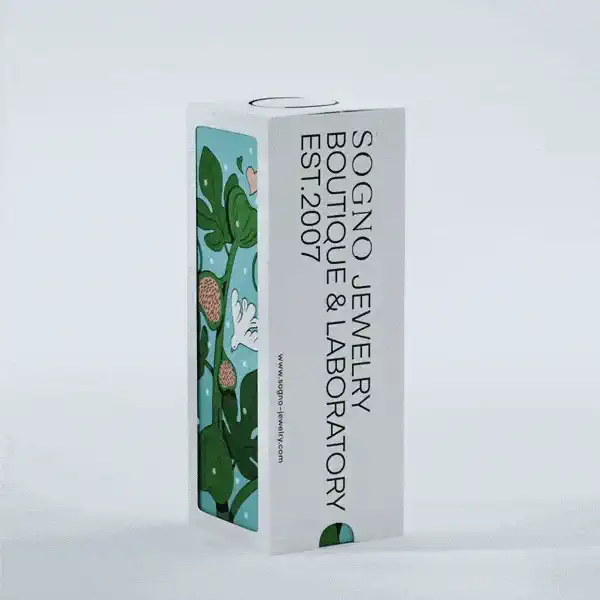
Natural Concept Perfume Design Ideas: Tell Your Brand Story
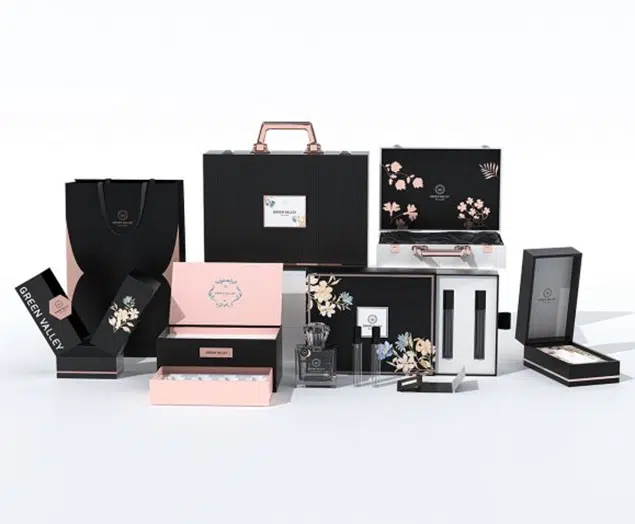