Is EVA or EPP Used for Drone Liner Packaging?
As is well known, traditional drone inserts are generally made of EVA material, which, although being a shock-resistant material, has some drawbacks. EVA is a single foam-molded product with low toughness and a soft surface, making it susceptible to scratches and affecting its appearance. It has weak tensile strength, making it unsuitable for products with strong pulling forces. Additionally, EVA has a low melting point and cannot withstand higher temperatures. The material produces an odor and cannot completely decompose or degrade, causing environmental pollution when discarded in the wild. Furthermore, EVA is prone to absorbing water, is not corrosion-resistant, and its surface is difficult to clean, making it challenging to remove oil and stains.
With the rapid development of technology, Expanded Polypropylene (EPP) material has emerged as a better alternative. EPP polypropylene offers exceptional features such as lightweight, abundant raw material sources, cost-effectiveness, excellent heat resistance, chemical resistance, and recyclability. It is currently the fastest-growing environmentally friendly thermoplastic material globally.
EPP Production Process
First, through specific formulations, diverse-colored PP particles are obtained. Then, foaming and other processes are applied to achieve 5-60 times foamed PP particles, which are then heated with steam to produce the final product. The EPP multiple options range from 60 times, 45 times, 30 times, 20 times, 15 times, 11 times, to 8 times, with higher multiples indicating lower hardness and better cushioning performance.
Advantages of EPP Products
Energy Absorption: EPP products possess a unique cellular structure that absorbs scattered energy through gas stagnation and compression, resulting in excellent anti-compression energy absorption properties. They are widely used in packaging backpacks for DJI drones, car bumpers, and cushion packaging.
- Stable Size and Shape Recovery: EPP products can undergo multiple continuous impacts and flexural deformations and immediately recover their original shape without deformation due to their “memory” capabilities.
- Excellent Heat Resistance: EPP products can withstand temperatures up to 130°C.
- Good Low-Temperature Characteristics: EPP products perform well even at -30°C and are suitable for advanced thermal insulation materials.
- Reusable: EPP products are flexible and durable, making them reusable and less prone to breakage.
- Lightweight: EPP products are extremely lightweight, significantly reducing the weight of items and facilitating portability and transportation.
- Surface Protection: EPP products have semi-hardness and moderate flexibility, offering good surface protection and preventing scratches or damage to contacted objects.
- Good Insulation: The independent cellular structure of EPP products results in low thermal conductivity, providing excellent insulation properties.
- Low Water Absorption and Good Buoyancy: EPP’s closed-cell structure ensures long-lasting buoyancy with minimal water absorption, even in saltwater.
- Oil and Chemical Resistance: EPP’s chemical inertness allows its products to exhibit excellent resistance to oil and chemical agents.
- Reusable and Eco-Friendly: EPP is easily recyclable, decomposes naturally, and does not contain harmful toxins. Burning it does not produce toxic substances.
- Excellent Stability: EPP products exhibit outstanding durability, including resistance to UV exposure, physical damage, extreme temperatures (-30°C to 130°C), wear, and other harsh environments.
Currently, EPP material finds extensive applications in drones, precision instruments, electronics packaging, cushion packaging, food packaging, automotive interior materials, and more. DJI’s drone packaging, Huawei’s corner protection packaging, and LG’s anti-static card boxes for LCD displays are among the products manufactured by Shenzhen Haomi Living Technology.
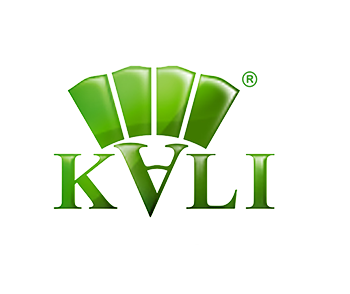
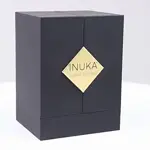
Top 10 Creative Cosmetic Packaging Design Ideas & illustrations 2023 | Luxury-Paper-Box.Com
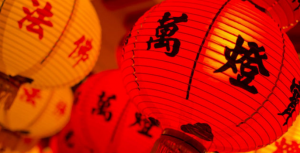
10 Customs Of The Spring Festival (Lunar New Year) You Need To Know
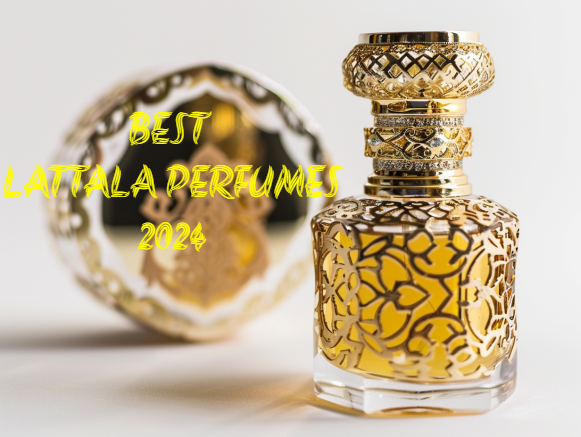
Top 10 Best Lattafa Perfumes for Women & Men in 2024
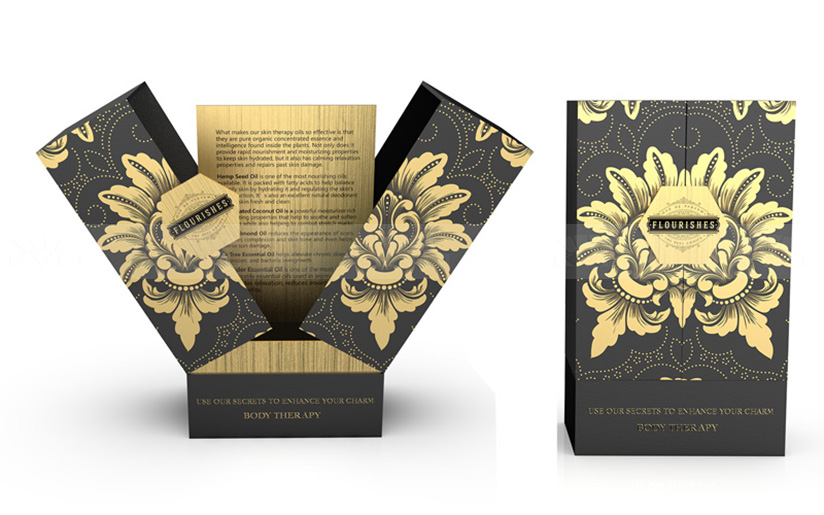