Reverse UV Pinting Guide: Princible, Advantage, Process, Requirements & More
Reverse UV process can produce different effects of high gloss and hoarseness on the surface of printed matter. The surface treatment links and processes of the printed materials are reduced. The printing machine can complete the process at one time, saving the processing process and the production time of the film covering. Reverse UV glazing can achieve the contrast effect that ordinary glazing can not do, which can make the printing effect of the printed matter better and more exquisite, and the printing quality even higher. Here is everything you should know about Reverse UV printing!
UV Printing Guide
The reverse glazing process can make the high brightness effect of mirror surface and the nonhigh brightness effect of matte or pitted surface exist on the same print at the same time, forming a stronger contrast in brightness, so that the glazing can achieve a better effect. At the same time, because the nonhigh light parts are printed by offset printing, the overprint is very accurate, which also ensures the printing accuracy of the high light parts.
Process Principle
The principle of “mutual exclusion” between coated UV varnish and base printing UV varnish (ink bucket UV varnish) is used to achieve the effect of bump texture and different gloss at one time, that is, coating varnish on the place without base oil to achieve the bright effect, and coating varnish on the place with base oil to achieve the matt effect. This process can achieve the change of light and dark (or wrinkle shrinkage strength) after UV glazing by controlling the amount of UV base oil or dot size.
There are three recommended printing sequences for the reverse glazing process.
1) UV color ink printing – UV irradiation curing – UV primer printing – UV irradiation curing – UV varnish coating – UV irradiation curing;
2) UV color ink printing – UV irradiation curing – UV primer printing – UV varnish coating – UV irradiation curing (no irradiation in the middle);
3) UV color ink printing – UV irradiation curing+(offline secondary printing)+UV primer printing – UV varnish coating – I-JV irradiation curing.
Advantage
The reverse glazing process is adopted to enhance the light resistance of the ink, increase the ability of the ink to prevent heat and moisture, protect the print, beautify the product and replace the film. The printing can be processed in two different ways.
Technological Process
① Conventional printing must be completed before glazing, and the ink must be completely dry or cured;
② Then, the non-high bright parts on the design draft are printed with transparent reverse ink by offset printing in online or offline way;
③ Then, the printing surface is coated with a UV varnish and cured in full version mode.
④ The varnish contacts with the reverse ink to produce a cohesive reaction, forming a small granular ink film in the non-bright parts to achieve the effect of a matt or pitted surface. The high brightness part without reverse ink forms a mirror high brightness effect
⑤ The reverse glazing process can make the high brightness effect of the mirror surface and the nonhigh brightness effect of matte or pitted surface exist on the same print at the same time, forming a stronger contrast in brightness, so that the glazing can achieve a better effect. At the same time, because the nonhigh-light parts are printed by offset printing, the overprint is very accurate, which also ensures the printing accuracy of the high-light parts.
Material Requirements
Smoothness
The paper with high surface smoothness is selected. The paper quality or rough surface and large oil absorption will reduce the glossiness of the printed matter surface and make the polishing effect not obvious.
Powder spraying amount
If the document is printed with ordinary ink, it is recommended that the online polishing process does not use powder spraying, or the water-based varnish can be coated offline. There is too much powder spraying on the printed matter, which affects the polish glazing to form a mirror without contrast with the particles. The effect is not strong.
Ink drying
When the printing must be fully dry, carry out the surface treatment. When the ink layer is not dry, the varnish may not be cured thoroughly and have no effect.
Prepress production
The pattern needs to be selected, the frosting effect part should be selected, the background color should be filled, and the bright place should be empty for film and publication.
Absorptivity
Select the paper with poor surface absorption, and the polishing effect of the paper with strong absorption is not obvious
Paper material
Paper with good surface quality shall be selected. The paper with poor surface color is easy to be exposed
Additive
For reverse UV process products, generally less UV curing agent is added, not more than 1%, which is not conducive to the reverse UV effect
Paper moisture content
Materials with moderate moisture content shall be selected. Paper with high moisture content is deformed and curled, and paper with low moisture content is easy to break when dry
Printing Precautions
1) The printing plate shall be baked or UV special plate shall be used.
2) The printing press shall not be directly exposed to sunlight.
3) The workshop temperature is kept at 20-25 ℃.
4) The roll gap must be adjusted after replacing the ink roller.
5) UV ink shall not be printed at the place where solidification, adhesion, smell, preparation/food contact are required.
6) The fineness and coarseness of texture, hand feeling, and oil feeling are related to such factors as front and rear UV light, printing speed, oil thickness and quality, printing pressure, and paper flatness:
-The effect of turning on the UV light before and after the OP oil: if the UV light is turned on after the OP oil and before the varnish, the texture has a frosty feel, the texture is obvious, showing a white effect, and the trachoma, that is, the dew varnish, has no (dry and wet reaction); When the UV light is turned on at the paper receiving place, the texture is oily, the matte feel is not obvious, and the trachoma, namely the dew oil, is obvious (wet and wet reaction);
– Effect of printing speed: if the printing speed is fast, the texture will be coarse, and the trachoma, that is, the dew oil, will be larger; If the speed is slow, the texture is fine, and the trachoma is less dew oil;
– The effect of thick oil: thick oil makes the texture more delicate; If the oil is thin, the texture is rough;
– The quality of the oil is different from the brand, and the effect is also different;
-The printing pressure is different, and the effect is different;
The surface flatness of the substrate is different, and the effect is different: if the surface is smooth, the texture is obvious; If the surface is poor, the texture is not obvious;
– Reverse UV oil – it is the parting oil and base oil; The base oil is the printing ink roller oil, and the surface oil is the varnish of the oil seat;
-Printing machine – only the printing machine with oil seat can be loaded
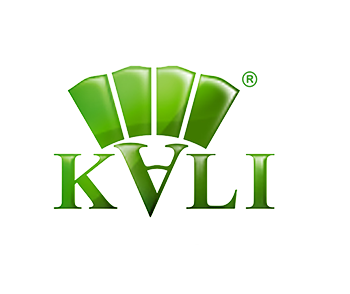
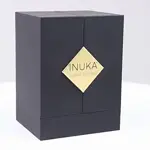
Top 10 Creative Cosmetic Packaging Design Ideas & illustrations 2023 | Luxury-Paper-Box.Com
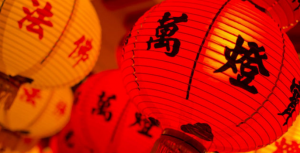
10 Customs Of The Spring Festival (Lunar New Year) You Need To Know
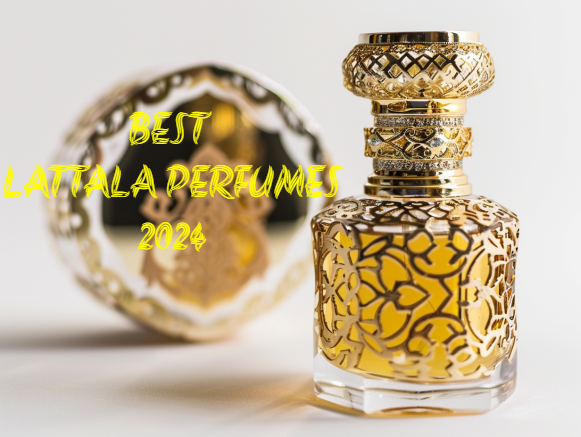
Top 10 Best Lattafa Perfumes for Women & Men in 2024
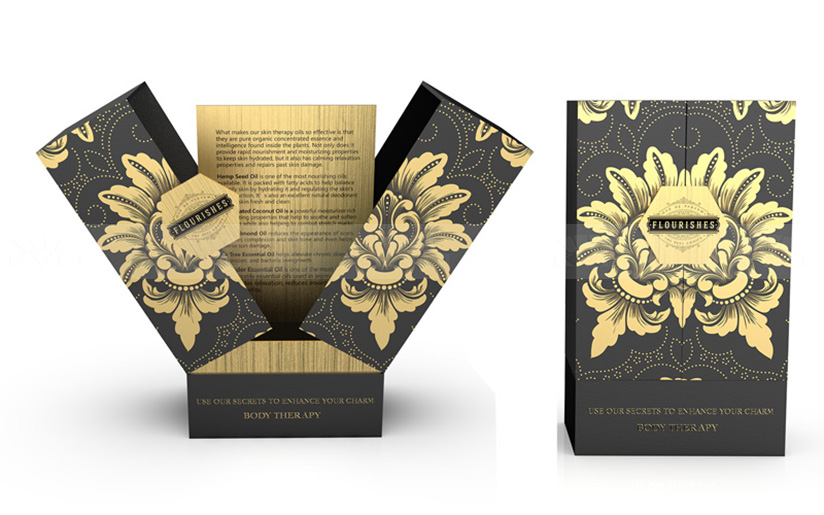
Top 10 Best Packaging Design Software 2023 (Free & Paid)
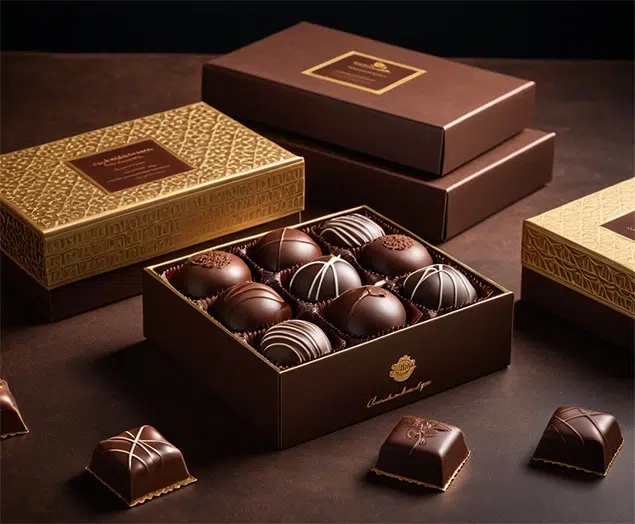
Best Chocolate Packaging Designs of 2025
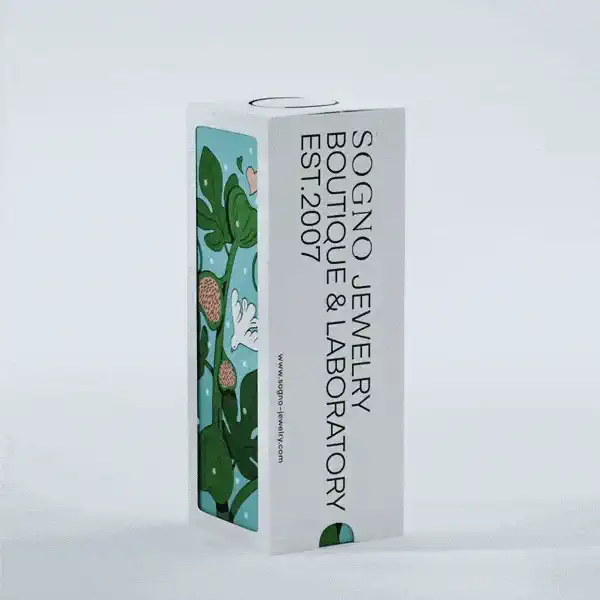
Natural Concept Perfume Design Ideas: Tell Your Brand Story
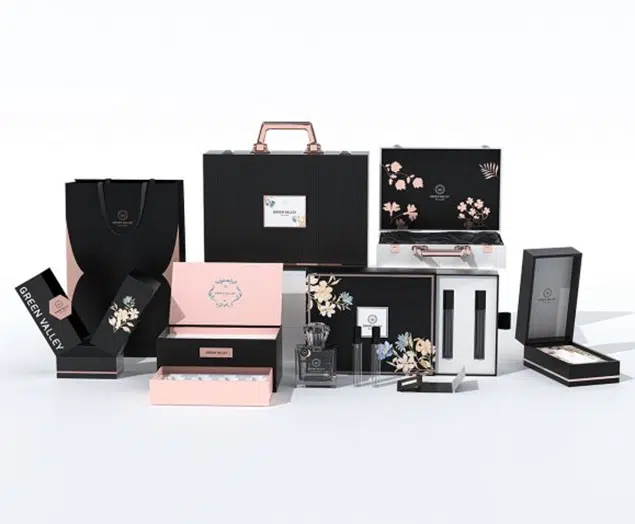